目前,在我国“碳达峰、碳中和”的“双碳目标”指导下,各工业均需要转变发展理念,向低碳化、绿色化发展,作为高温工业支撑的耐火材料行业也不例外。不定形耐火材料在制备过程中无需高温烧成,可以有效节约能源,再加上工艺简单、便于机械化施工等优点,是符合行业未来绿色发展方向的重要材料之一。作为不定形耐火材料的常见类别之一,耐火浇注料由于综合性能优异而被广泛应用于各种热工设备。在浇注料中加入水,首先可以使原料的混合均匀过程更加有效,并使浇注料砂浆更容易输送和成型;其次,水与浇注料中水硬性结合剂的反应,可以为材料提供必要的早期强度。这些水虽然在较低温度时可以稳定存在于材料内部,但随着温度的逐渐升高,它们又会以水蒸气的形式逸出。如果该过程不能顺利进行,往往会导致材料的结构损伤乃至灾难性破坏(爆裂),所以说防爆裂性能是影响浇注料使用效果的关键性能之一。以往对浇注料的施工性能、高温性能与抗热震性已有较多讨论,而对防爆裂性能的系统论述则较少。本工作就从浇注料的爆裂破坏机理、结合体系、防爆裂手段、测试手段、模拟研究等方面进行了介绍,并对未来研究作出了展望。
1 浇注料的爆裂破坏机理
依据目前的主流理论,施工完成的浇注料是非均质的整体材料,加热时各组分膨胀系数不同,却又相互约束不能自由膨胀和收缩,再加上受热区域和内部区域间温度梯度的存在,材料就会产生热应力。而浇注料中的自由水、结合水(主要来自于结合体系)在烘烤过程中变为水蒸气,也会在坯体内部产生压力。在浇注料的烘烤升温过程中,由于温度梯度等导致的热应力和内部水蒸气产生的压力共同作用,材料就有可能发生爆裂破坏(图1)。在此基础上,有研究者提出热应力为提供了爆裂所需的大部分能量,而水蒸气压力在孔隙中的积累只是作为裂纹扩展开始的“触发器”。另外,使用外部热源加热浇注料时发生的“水分阻塞”现象也常被认为会加剧结构的爆裂破坏(图2)。
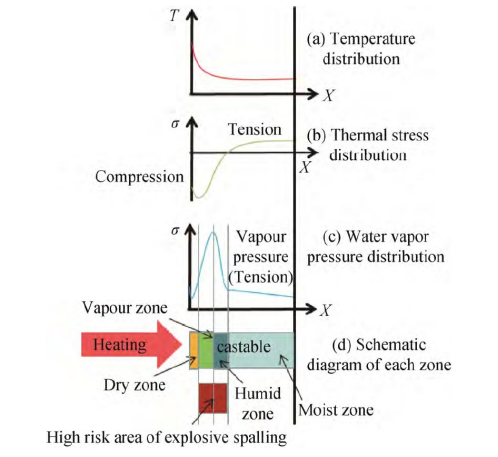
图1 单面加热浇注料爆裂破坏机理[6]
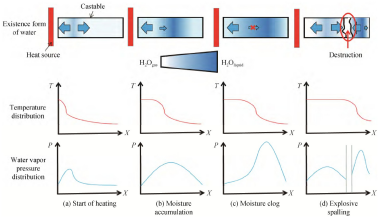
图2 浇注料爆裂破坏中的“水分阻塞”现象示意图
在以上2种主要破坏机制中,虽然热应力破坏机制十分重要,但由于测量困难且理论计算复杂,以致其在浇注料中的相关研究较少;而水蒸气产生的压力则由于检测相对容易,研究成果也较多,因此目前有关浇注料防爆裂的研究多沿着“防止水蒸气压力累积”的思路。而在讨论水蒸气的产生对浇注料结构造成的压力时,最常用的就是Antoine方程(0~374℃范围内的液–气平衡条件下适用),公式如下:

其中:Pv为水的饱和蒸气压(Pa);T为温度(K),A、B、C为基于经验的无量纲常数(对于水,A=23.33;B=3 841.22;C=–45.00)。将式(1)计算出的水的饱和蒸气压随温度增长的曲线绘于图3,结合文献数据(浇注料的生坯强度一般介于0.6和2.3 MPa之间),发现在160℃左右水蒸气能够产生的压力已经可能大于材料的强度,足以引发爆裂。因此常常需要采取合适的防爆裂手段使浇注料内部水蒸气能够及时释放,以减少其压力累积导致的结构破坏。
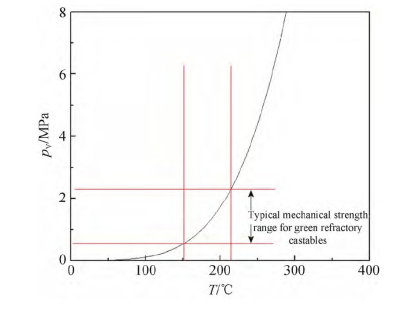
图3 由Antoine′s方程计算出的水的饱和蒸气压随温度增长曲线
2 浇注料结合体系与防爆裂
浇注料防爆裂的研究成果主要基于“防止水蒸气压力累积”的思路,浇注料结合体系虽然众多,但有较大爆裂风险的主要是含水结合体系,如铝酸钙水泥(CAC)结合体系、可水合氧化铝(HA)结合体系、溶胶结合体系和氧化镁结合体系。按照以上分类,介绍各类浇注料的结合机理、典型结构特点与抗爆裂性能。
2.1 铝酸钙水泥结合体系
使用铝酸钙水泥结合的浇注料具有施工性能良好、生坯强度高等优点,因此该体系是目前最常用的浇注料结合体系之一。铝酸钙水泥的低温结合作用主要来自于水泥与水发生水化反应形成的铝酸钙水化相(如CAH10、C2AH8、C3AH6)和氧化铝凝胶(AH3)结合网络。铝酸钙水泥的水化过程可分为溶解、成核、沉淀3个阶段:1)干燥的铝酸钙水泥颗粒与水接触后,颗粒表面水化,生成少量水化产物、立即溶解在水中并释放出钙和铝离子,使新表面暴露出来继续进行溶解过程,水中钙、铝离子浓度持续增加,直至达到饱和极限为止;2)溶解阶段后,铝酸钙水泥的水化产物成核,并逐渐达到临界尺寸和数量;3)成核结束后,水化产物发生析出沉淀,浇注料机械性能随之增加。铝酸钙水泥的结合强度来自于各种水化相,这使其有较好的低温结合强度,但在烘烤升温过程中,水化相通常先会发生转化(如CAH10、C2AH8转化为更稳定的C3AH6),继而会发生脱水反应(300℃左右),这既会破坏原有的结合结构,又会由于水蒸气的排出而进一步增加材料的气孔等缺陷,使材料有较大的爆裂风险,因而必须谨慎选择水泥结合浇注料干燥过程的升温曲线。为了解决这个问题,研究者开发了低水泥浇注料(LCC)和超低水泥浇注料(ULCC),减少了结合体系中水泥和水的用量,并引入了防爆剂,取得了一定成果。虽然铝酸钙水泥结合的浇注料存在爆裂风险,但是由于水泥的水化产物众多,且它们的分解温度不一:低温稳定水化相CAH10的分解温度在120℃左右,C2AH8的分解温度在170~195℃左右(低温养护后快速升温才能观察到直接分解);而在110℃烘后,水泥的水化相主要是C3AH6和AH3,在250~300℃之间这2个相分别会分解为C12A7和Al O(OH),而后者在678℃左右又会进一步转化为Al2O3并释放出水。水泥结合浇注料中的水分是逐次排出的,这就减小了水蒸气的排放峰值;且大部分水化产物分解温度都不太高,这也使水蒸气的压力不会太大,因此与其他几种水合结合浇注料相比,铝酸钙水泥结合的具备相对优异的抗爆裂性能。
2.2 可水合氧化铝结合体系
由于使用铝酸钙水泥结合时引入了较多的氧化钙,高温下可能会与其他物质反应生成低熔相而劣化浇注料性能,研究者开发了可水合氧化铝结合体系。可水合氧化铝是结晶度较低的一类亚稳态氧化铝的统称(如κ-Al2O3、θ-Al2O3、ρ-Al2O3),具有水化活性,其中又以ρ-Al2O3的相关研究最多。可水合氧化铝的结合作用也是来自于水化反应,以ρ-Al2O3为例,其基本水化过程可分为2步[19,20]:1)可水合氧化铝颗粒的潮湿表面向水中溶解,形成Al(OH)4-离子(Al2O3·n H2O(0.2≤n≤1)+H2O→Al(OH)4-+H2O);2)在短暂的诱导期后,Al(OH)4-由于浓度逐渐升高而在附近区域达到饱和,使拟薄水铝石(β-AlOOH)和拜耳石(β-Al(OH)3)从水中析出(Al(OH)4-+H2O→β-AlOOH+β-Al(OH)3),并在可水合氧化铝颗粒表面形成无定形凝胶层。这种粘性凝胶可以渗透到颗粒间的空隙中阻碍其运动,并使整个分散系统保持稳定,从而为养护后的浇注料提供施工必需的生坯强度。另外,进一步研究表明:可水合氧化铝的水化过程还会受到反应条件(温度、pH等)、其他原料成分等因素的强烈影响[20,21],因此可水合氧化铝结合的各类浇注料可能具有不完全相同的水化过程,所以对相关过程、机理的深入探究仍有较大的科学价值。可水合氧化铝的应用固然可以使某些材料体系满足对高温性能的需求,但同时也使材料的抗爆裂性能相比于铝酸钙水泥结合体系显著下降。究其原因,虽然可水合氧化铝水化产物的初始分解峰值温度(150~300℃)并不算太高,但首先有些水化产物的分解温度相对集中,导致此时材料有较大的水蒸气排放需求;其次这些水化产物大部分是渗透性不佳的凝胶状物质,在完全分解(400~600℃)前都会对材料内部气孔通道起到堵塞作用,这也就导致浇注料的透气性不好,内部水蒸气难以排出而残留至较高温度,进一步增大了对结构的压力;再次,可水合氧化铝水化提供的结合强度也不如铝酸钙水泥;最后,使用高比表面积的可水合氧化铝又带来了高需水量,也就是说受热时浇注料有较大的水分排放量。正是由于自身抗爆裂性能不佳,使用此类浇注料时更要注意选取合适的防爆添加剂,并十分严格地控制烘烤曲线,以尽量减小加热过程对材料结构的破坏。
2.3 溶胶结合体系
使用铝酸钙水泥结合时,材料常有高温性能方面的问题;而使用可水合氧化铝结合时,材料又不具备良好的抗爆裂性能,因而研究者又开发了溶胶结合体系,其中又以硅溶胶的研究、应用最为成熟。硅溶胶颗粒内部是硅、氧原子构成的网络结构(—Si—O—Si—),而其表面则被硅羟基(—Si OH)和羟基(—OH)所覆盖。当其用作浇注料的结合剂时,硅溶胶颗粒可以通过胶凝、絮凝等机制将自身互相连接起来(溶胶硬化),从而给材料提供早期强度。具体说来,硅溶胶结合的胶凝机制源于溶胶颗粒表面的硅羟基之间直接发生脱水反应而形成的硅氧烷(—Si OH+HOSi—→—SiOSi—+H2O);而絮凝机制则需要絮凝介质发挥桥接作用,也就是说该机制中不同硅溶胶颗粒是通过絮凝介质相互连接,从而产生沉淀并为材料提供强度的。铝酸钙水泥和可水合氧化铝都需要水化产物给浇注料提供早期强度,但这些水化产物的高温分解又会使水以气体形式从材料内部释放出来,这就导致浇注料不仅在加热升温阶段有特殊的操作要求,往往还需要防爆添加剂的配合作用。而硅溶胶硬化时不会生成水化相,而会形成一种多孔结构(图4),这种结构虽然不能使浇注料具有较高的生坯强度,却可使其具备良好的透气性(约比铝酸钙水泥结合高3个数量级)。因此硅溶胶结合体系的应用可以让浇注料内部的水分更加安全、快速地排出,如Gordeeva等将未经初步干燥的硅溶胶结合浇注料直接进行高温热处理,亦未发现明显的爆裂破坏。
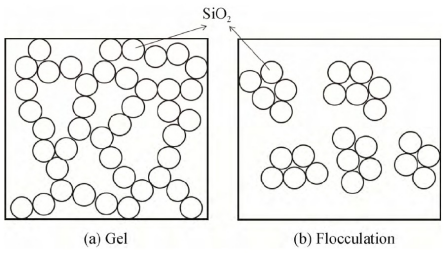
图4 硅溶胶硬化结构示意图
2.4 氧化镁结合体系
与以上3种应用范围较广的结合体系不同,氧化镁结合体系一般仅用于镁质、铝镁等少数几种浇注料中,但该结合体系中也含有较多的水,因而也有爆裂的风险。氧化镁的低温结合作用也来自于水化反应(MgO+H2O–→Mg(OH)2),即氧化镁水化产生的氢氧化镁填充于浇注料内部的空隙中,从而使其周围接触的不同颗粒连接起来,并使浇注料具备早期强度。具体水化反应过程与水泥相似,以氧化镁在水中的溶解开始,氧化镁颗粒表面被H+质子化形成Mg(OH)+,然后溶液中带负电的OH–被静电吸引到颗粒表面的Mg(OH)+周围形成Mg(OH)+·OH–;然后Mg(OH)+·OH–中的Mg2+和OH–又会被逐渐释放到溶液中,直到浓度达到饱和;最后氢氧化镁就会以固体的形式从溶液中沉淀出来。由于氧化镁的水化产物与自身密度相差较大,ρ(MgO)=3.5 g/cm3;ρ[Mg(OH)2]=2.4 g/cm3,该水化反应伴随着较大的体积膨胀(约2.5倍),如此大的体积膨胀往往会在浇注料内部产生裂纹;另外,水化产物氢氧化镁的高分解温度(380~420℃)和微结构的低渗透性,还可能导致材料内部存在较高的水蒸气压力,因此以氧化镁为结合剂的浇注料本身存在较大的爆裂风险。正是由于氧化镁结合浇注料易于爆裂,添加剂等防爆裂手段的采取也是该体系浇注料能够正常应用的重要保证之一。由上述分析可知,浇注料的抗爆裂性能与其使用的结合系统密切相关(表1),因此在选用结合剂时需要依据实际情况进行综合考虑。
表1 典型浇注料含水结合体系的抗爆裂性能比较
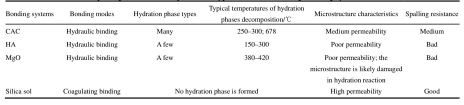
3 浇注料防爆裂手段及其效果
对小尺寸样品的研究表明:除凝聚结合的浇注料外,使用其他含水结合系统(即水合结合)的浇注料大多都有较高的爆裂风险;而对大尺寸样品或者实际的浇注料产品,即使是具有高渗透结构的硅溶胶结合浇注料也会在某些急速升温状况下发生爆裂,因此,对浇注料防爆裂性能的提升常常是必要的。浇注料爆裂的发生与水分的排出过程密切相关:首先,在高温的作用下,浇注料内部的水(结合水、自由水)变为气态;然后,生成的气态水通过内部孔隙通道向其他区域迁移,并最终从材料表面逸出。因此降低浇注料爆裂风险(提高抗爆裂性能)的手段常从这2个过程的调控入手。对于前一过程,水蒸气的产生状况主要受到局域温度(温度分布)和水分来源(水合物、自由水)的影响,其中决定水分来源的主要因素就是结合体系,而材料内部的温度分布则与采用的加热方式有关。对于后一过程,调控思路就是改变水分的排出路径,即改变浇注料中的微观孔隙通道,具体手段又可分为2类:与物理堆积结构有关的粒级配比设计以及与化学反应结构有关的基质成分设计。虽然前者可以改变水分排出通道的结构,从而在一定程度上影响浇注料的抗爆裂性能,但该方法的使用还可能对浇注料的其他性能产生不利影响,因此多数研究者还是倾向于使用后一类方法(即加入添加剂)来改变浇注料内部的孔隙状态,从而提升其抗爆裂性能(各因素影响防爆裂性能的主要机制见表2)。
表2 各项因素影响浇注料水分排出的主要机制

3.1 添加剂
3.1.1 发气型防爆剂
发气型的防爆添加剂需要通过化学反应产生大量气体,这些气体在浇注料固化过程中逸出时,会在材料内部留下孔隙通道(开口气孔),从而起到防止爆裂的效果,金属铝、有机发泡剂均属于此类。1)金属铝。粉末状的金属铝是铝酸钙水泥结合浇注料中的传统防爆添加剂之一。浇注料中的铝遇水,会产生氢氧化铝凝胶和氢气,并伴随大量发热(Al+3H2O→Al(OH)3+3/2H2↑)。该反应本身在常温下速率慢,但如与碱共存则会生成可溶于水的络离子,从而加快反应速度。因此,金属铝的防爆机理是通过前述反应先产生大量H2,紧接着H2向坯体外部逸出,形成大量开口气孔,提高浇注料透气性,从而为干燥时水蒸气的排出提供了通道。另外,Li等[42]使用纤维状的金属铝作为Al2O3–SiC–C质铁沟浇注料的防爆剂,也取得了较好的使用效果。金属铝的用量合适时,可以起到良好的抗爆裂作用;但一旦加入过多,浇注体就可能鼓胀、层裂甚至坍塌破坏。而铝与水的反应状况与原料的活性、细度、纯度及温度等因素都有很大关系,所以使用实验室数据为工业实践进行指导时不总能取得良好的效果。同时,粒度较小的金属铝自身有易燃易爆的问题,造成了原料运输和储存成本的增加;而产生的氢气也有遇火燃烧、爆炸的危险,所以现在的应用趋势是尽量使用其他防爆剂,而避免使用金属铝。2)有机发泡剂。除铝粉外,水泥结合系统中常用的发气型防爆剂还有有机发泡剂。有机发泡剂的防爆原理是发泡剂与水泥、水反应生成钙盐,钙盐分解产生气体,气体排出时留下通道,从而减少浇注料升温时水蒸气的压力积累。如最常用的偶氮二甲酰胺(C2H4N4O2,AC),其具体作用机理[43]是在高铝水泥及水的共同作用下,本不溶于水的偶氮酰胺生成钙盐而溶解(C2H4N4O2+Ca(OH)2+2H2O→Ca(C2N2O4)+2NH4OH),之后钙盐随温度和时间的变化而又产生N2、CO2、NH3等气体(3Ca(C2N2O4)+3H2O→2N2↑+3CO2↑+2NH3↑+3CaCO3),继而在浇注料中形成10μm左右的开口排气孔,并提高材料的透气性。由于有机发泡剂的反应不像铝粉那样剧烈,因此浇注料不易出现鼓胀和细粉上浮的问题,而且其反应也不会因温度的差别而产生很大变化,施工时更易掌握,也就是说使用有机发泡剂时,浇注料的性能更加稳定可控。
3.1.2 孔隙残留型防爆剂
与发泡型防爆剂不同,孔隙残留型防爆剂虽然在较高温度下也可能有气体生成,但其主要的防爆机理并不依赖于此,而是基于防爆剂自身占据的空间在受热时产生的孔隙通道(不一定与其他气孔连通)。以典型的孔隙残留型防爆剂——有机纤维为例,在浇注料的烘烤过程中,均匀分散的有机纤维受热收缩、熔融或炭化,形成微细的狭长气孔,从而让内部水蒸气可以迅速释放出去,避免在浇注体内积聚形成较大压力导致爆裂。与铝粉相比,加入有机纤维后,低温时浇注料内没有化学反应产生,施工过程容易控制,影响因素较少,没有危险性。虽然有机纤维的使用有时存在不易分散或加入量多影响强度等问题,但相比于带来的优点,一般认为,其使用对浇注料的性能利大于弊,再加之其原料来源也较广泛[44],因此是目前最普遍应用的防爆剂之一。当然,由作用机理可知,有机纤维形成的孔隙结构受到纤维性质(如熔点、分解温度等)及形貌的强烈影响,所以要想取得较好的使用效果,必须依据不同浇注料的具体情况选择性质适宜(使水分可以在较低温度释放)、长度等形貌合适(使更多内部气孔相互贯穿,有效提高透气性)的有机纤维作为防爆剂。
3.1.3 新相构成型防爆剂
除了以上2种较为传统的防爆剂,研究者们还开发了新相构成型的防爆剂。不同于发泡型防爆剂通过产生的气体对结构挤压产生的孔隙,也不同于孔隙残留型防爆剂通过空间占据残留下的孔隙,此类防爆剂通过化学反应产生的新相直接改变浇注料基质中的孔隙结构。不仅如此,产生的新相还可能影响到水蒸气的生成过程,此类防爆剂可以较显著地改善浇注料的抗爆裂性能。1)新型通用防爆剂。近年来开发的一些新型通用防爆剂就属于新相构成型,如增渗活性剂(ACM,其成分占比(质量)中,Al2O3为39%~43%、CaO为12%~15%、MgO为6%~20%,烧失掉的质量为24%~30%)就是其中之一[41,45]。ACM中含有螯合剂、分散剂、钙盐与镁盐,螯合剂是有机酸的铝盐,能够与单个金属离子(如水泥溶于水产生的Ca2+)形成多个键并产生复杂的环状结构。依据目前研究结果,该添加剂在抑制结晶水化相生成的同时,可与铝酸钙水泥、可水合氧化铝等多种浇注料结合剂反应生成无定形凝胶状水化产物。以铝酸钙水泥为例,该添加剂的加入可改变其水化反应顺序,从而最终生成Ca O·Al2O3·H2O(CAH)凝胶,而不是传统的CAH10、C2AH8、C3AH6和AH3等相。这种凝胶化合物的脱水反应会在较窄的温度范围(100~150℃)内进行,首先这会导致水分的排出更快;其次由于此时温度较低,虽然水分的排出量多,但内部积聚的压力并不高,因此也会使浇注料的干燥过程更加安全,Bezerra等[45]的实验结果也验证了这个判断——升温速率为20℃/min时,不含防爆添加剂的铝酸钙水泥/可水合氧化铝结合浇注料试样均会发生爆裂,而ACM的加入则可以有效抑制该现象的发生(使用效果好于有机纤维)。但使用该添加剂也有负面效果,即在提升材料防爆性能的同时,又可能对浇注料的施工性能、生坯强度等产生不利影响。浇注料中使用的碱式乳酸铝[AHL,Al(OH)3–x·CH3CHOH(COO)x·n H2O]是一种由氢氧化物离子聚合而成的多核络合物,也是新相构成型防爆剂之一。在与其他材料组分的反应可以忽略时,研究表明:升温过程中,碱式乳酸铝会发生凝胶化而形成新相,从而在基质中形成网片状微小裂纹通道,所以其加入会改善浇注料的透气性和抗爆裂性能。但含碱式乳酸铝的浇注料干燥后容易形成永久裂纹,影响材料的其他性能[43]。乳酸铝(碱式/非碱式)还可以与浇注料中其他成分发生反应而形成新相,如Miguel等[37]与Fini等[38]则分别制备了含碱式乳酸铝(AHL)和乳酸铝[AL,Al(CH3CHOHCOO)3]的具备优异抗爆裂性能的氧化镁结合高铝质浇注料,并分析了它们的作用机理。研究发现,碱式乳酸铝和乳酸铝对浇注料中氧化镁的水化过程有类似的影响,因此它们对抗爆裂性能的提升机理也类似:首先,碱式乳酸铝或乳酸铝可以在氧化镁颗粒表面生成层状双氢氧化物[Mg6Al2(OH)16(OH)2·4.5H2O/Mg6Al2(OH)16(CO3)·4H2O](类水滑石结构),从而可以抑制氧化镁的水化反应及水镁石的形成,进一步可以减少氧化镁水化膨胀带来的结构破坏(对材料强度有利);其次,类水滑石结构的层状特征在氧化镁结合浇注料的干燥升温过程中也起着重要作用,层状结构的存在不仅使浇注料具有较高的透气性,此结构还使材料内部水分(游离水、层间结构水)由于结合能的不同而在较宽的温度范围(50~300℃)内释放,从而将与水蒸气压力相关的爆裂风险降至较低水平。Pinto等[30]比较了有机纤维、乳酸铝(AL)、含硅防爆剂和增渗活性剂ACM在氧化镁结合高铝质浇注料中的防爆效果,也发现了乳酸铝和ACM对材料防爆裂性能的明显提升(20℃/min升温时亦未出现明显爆裂),究其原因,可能是由于这2种添加剂反应生成的类水滑石相在低温下允许层间水排出,也可能是由于凝胶相在较低温度发生分解,从而在微观结构中形成大量孔隙通道,最终使含这2种添加剂的浇注料都能够在80~123℃时释放出更多的水,并改善材料的防爆裂性能。Bezerra等[45]则探索了乳酸铝(AL)对可水合氧化铝结合浇注料防爆性能的影响。研究结果表明:该添加剂与增渗活性剂ACM的作用机理相似,因为其诱导了结合剂水化反应的变化及新相的生成。某些新相的生成对浇注料抗爆裂性能的提升是有利的,如乳酸铝反应生成的凝胶状物质分解后可以生成更多的渗透路径;而乳酸铝与铝酸钙水泥(作为添加剂)中的氧化钙反应还能生成分解温度低(130℃)的乳酸钙(CaC6H10O6·5H2O),可使浇注料内部水分在较低温度下释放,从而减少水分排出对材料结构的破坏(此时水蒸气压力较小)。但结合剂水化反应发生改变以后,又会导致浇注料的固化时间延长,且生坯强度下降。然而,将0.5%(质量分数)的铝酸钙水泥添加到含乳酸铝的可水合氧化铝结合浇注料中时,这些负面影响可以降至最小,即此时材料具备适当的强度和透气性,可以在相对较低的温度(小于200℃)释放出较多的水分。在模拟实验中,即使加热速率提升为20℃/min时,该组配方制备的浇注料也没有发生爆裂。2)专用防爆剂。除了通用型防爆添加剂外,还有一些新开发的特定结合系统专用防爆剂也属于新相构成型。以氧化镁结合系统为例,在其中加入合适的羧酸时,就可以通过形成新相来控制结合剂氧化镁的水化过程并影响材料的微观结构,从而提高浇注料的防爆裂性能。如Dos等[32]的研究发现在铝镁浇注料中加入甲酸可以促进具有层状结构的类水滑石相的原位生成,该结构的存在可以增强材料的透气性并使水分可以在更宽的温度范围内排出,从而提高材料的抗爆裂性能;Souza等[36]则研究了乙酸对浇注料中氧化镁水化过程的影响,结果表明:乙酸的加入可以促使具有柔韧性的独特氢氧化物晶体的生成,使氢氧化镁生成时发生的膨胀可以被较好地被容纳于浇注料微观结构中,从而抑制了材料在养护过程中的开裂,并有利于抗爆裂性能的提升。不同防爆添加剂具备不同特点(表3),在实际使用中必须与浇注料的特性结合进行综合考虑,才能使其正常发挥作用。
表3 浇注料典型防爆添加剂及其优缺点
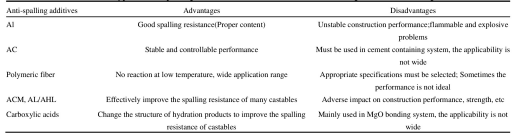
3.2 加热方式
在浇注料干燥过程中,气态水的产生除与物相特性有关外,还与区域温度有关。而浇注料中的区域温度或者说温度分布与加热方式紧密相关。因此,使用合适的加热方式也能有效降低材料的爆裂风险。浇注料的传统加热方式有火焰加热、热风加热、电阻加热等,从加热过程进行分析,其都是先将其他形式的能量(如化学能、电能)转化为热能,而后将热量输送到材料附近,对其从外到内逐步加热,因此均属于外部热源(EHS)加热。使用此类加热方式时,无论是采用单热源(如单面烘烤等)还是多热源(如电阻炉加热等,可简化为双面加热定性分析)布局,材料内部总是存在较大的温度梯度。由于传统加热方式有难以克服的固有缺陷,为降低浇注料的爆裂风险,研究者们又开发了新型加热方式用于浇注料的烘烤,其中的典型代表就是微波加热。微波是频率范围在300 MHz~300 GHz(波长范围1.0 mm~1.0 m)的电磁波,而微波加热则与物质在高频电场中吸收能量的能力有关。如由具有正极和负极的极性分子组成的介电陶瓷暴露于微波的高频电场时会出现偶极极化和离子传导,从而导致这些有序分布分子的瞬时振动。最后,由于分子的摩擦作用,会在材料内部的整个空间内产生热量(即材料被整体加热)。微波加热的优点[13]有:1)加热速率高,同时加热整个部件(水分宏观上呈现出向外的单向输运,避免了由外而内加热时导致的“水分阻塞”),从而降低能耗,缩短工序所需时间;2)电磁波可以深度渗透,从而促进了待干燥材料中温度的均匀化(不同方式加热时浇注料内部典型温度分布见图5);3)可以进行瞬时、精确的电子控制。另外,相比于直接使用燃料燃烧产生的火焰进行加热的方法,还有不产生2次废物、加热更加清洁的优点。关于微波加热在浇注料中的应用实例,Czechowski等[46,47]就比较了低水泥高铝质浇注料使用微波加热与传统加热方法对材料性能的影响,结果发现,微波加热对于低水泥耐火浇注料预制件的干燥和脱水特别有用,600℃保温5 h的常规方式脱水和约520℃保温2.5 h的微波方式脱水所得到的材料几乎相同,不仅材料均完全脱水而未发生爆裂,且强度演变、显气孔率、矿物相组成均类似。虽然微波加热有如此多的优点,是传统加热方式一种有前景的替代方法。但是,微波干燥的大规模推广尚存在挑战。首先,微波加热一般是在炉膛中进行的(过量微波对人体有害),因此,对于部件尺寸有要求,对于非预制件或大型部件的加热存在较大困难,施工灵活性有所欠缺;其次,微波加热时必须根据部件的不同尺寸设置不同加热参数(微波功率选择与变化曲线、加热时间等),而这种参数的设置由于没有可靠资料以供参考很大程度上只能依照操作者的自身经验,因此可能造成人员、部件尺寸等因素均会对最终材料产生较大影响,假如参数不能合理设置,不仅不能完全发挥微波加热本身的优势,还会使不同尺寸产品的性能有较大差别(各型产品性能不能一致)。
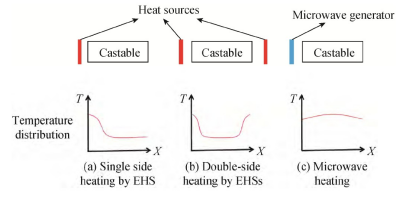
图5 浇注料内部温度分布示意图
4 浇注料干燥过程的测试
浇注料常由于制备参数、配方等的改变而具备不同的抗爆裂性能,在评估相关性能时,不可能将所有材料均制备为实际的耐火部件进行工业试用,这样不仅耗费了时间、资源,而且增加了试验成本。为了在实验室中全程观测、分析浇注料的水分排出过程(包括爆裂),并有效评估其抗爆裂性能,研究者们开发了许多测试手段。
4.1 热分析与爆裂实验
综合热分析(TG–DSC/DTA)是研究结合剂脱水动力学和浇注料干燥行为的传统方法之一,其中,热重分析(TG)由于可以直观反映出材料的水分排出状况而显得尤为重要,因而在不能使用常规综合热分析仪器时(如由于尺寸过大),单独利用专门的热重分析仪也能表征浇注料的许多特征。进行综合热分析时,可以从测试结果得到浇注料整体水分排出的速度和阶段(自由水释放、水化产物分解等)、水分快速排出的温度范围、发生爆裂时的温度等信息。爆裂实验就是将测试样品放入保持在一定温度的加热炉中,然后观察样品经过特定时间后是否发生爆裂破坏。该实验评估了浇注料在给定条件下水分快速释放以及适应高热应力引起的微观结构变化的能力,突出了材料的温度敏感性,可用于改变配方时的比较。但得到的结果没有提供任何关于浇注料固有参数(即含水量、透气性等)与外部条件(固化温度/时间、炉温、试样尺寸等)之间关系的信息,因此难以在探究爆裂发生机制时发挥作用。另外,尽管小样品也可能发生爆裂破坏,但根据实践经验,对于更大的浇注料坯体,爆裂通常发生在距离坯体表面不足100 mm的位置。Luz等[13]认为:使用100 mm×100 mm×100 mm的立方浇注料或600 mm×600 mm×350 mm的大块浇注料进行抗爆裂实验比较合适。而国家标准GB/T 36134—2018《不定形耐火材料抗爆裂性试验方法》,推荐的样品规格为φ80 mm×80 mm的圆柱状,也可以与相关方协商确定(如使用边长为50 mm的立方体),这可能是考虑到实际制样时存在的困难,在保证实验结果可靠性的前提下,在样品尺寸要求方面有所降低。
4.2 水蒸气压力的原位测量
浇注料的实际爆裂过程十分复杂,因为材料加热过程中,热、水、化学和机械等因素同时作用并相互影响,如产生的缺陷不仅有助于增加透气性,使内部水分易于排出并减少水蒸气压力的积累,从而减少爆裂的发生风险;同时,缺陷的存在还降低了浇注料的机械强度,又使爆裂易于发生。因而为了加深对爆裂过程的了解,一些研究人员提出了在浇注料的加热阶段中原位测量材料内部的温度和水蒸气压力。如文献[9,11,48]就分别使用压力引管/热电偶与应变片/热电偶原位测试了浇注料加热时内部的蒸气压与温度分布,均为对浇注料爆裂机理的进一步深入研究做出了自己的贡献。虽然传感器收集浇注料内部压力等数据的相关研究已有一定成果;但传感器的存在可能会改变材料性能(在附近形成裂纹或孔隙等缺陷),从而影响到测量结果的准确性,如放置传感器导致的缺陷可能成为水蒸气的逸出通道[49]。浇注料微观结构固有的异质性还会导致水蒸气流动路径存在随机性,从而可能导致压力分布不均匀。为了提高测量结果的可靠性,除了需要对同类试样重复测试以减少结果随机性外,还必须尽量减小传感器对浇注料干燥行为的影响,如Fey等[50]就使用了自制的新型压力传感器以期获得更加准确的实验结果。
4.3 水分原位观测新技术
除了以上几种较传统的测试手段外,随着测试技术的不断发展,为原位观测材料中的水分分布,研究者们还使用了许多先进的检测手段,如磁共振成像(MRI)、核磁共振(NMR)、X射线计算机断层扫描、中子照相技术和中子层析成像技术等。磁共振成像作为一种成像方法,扫描仪中的磁铁可以通过磁场作用于浇注料中带正电的氢离子(H+)并使其以相同的方式旋转。因此,改变扫描仪中外加磁场的强度和方向,质子的自旋方向也可能会随之改变,从而可以构建不同的层以分析材料微观结构。如Oummadi等[51]就使用了此项技术检测了氧化铝和高岭土基样品(长度40 mm,高度和宽度15 mm),发现磁共振成像可以提供样品生坯内部关于水分宏观分布的信息(空间分辨率小于0.5 mm),如水含量梯度及干燥前沿等。核磁共振也是一种可以表征氢位置的技术,因此可以无损检测浇注料生坯中的水分分布。正如Stelzner等[8]描述的1H-NMR测试原理,氢原子核(质子)在水中的含量丰富,而静态强磁场可用来研究质子的弛豫现象。原子自旋的固有属性使其倾向于排列在静态磁场的平行方向,从而导致较小的净磁化;这个净磁化可以通过射频(RF)激发,而它们恢复到热平衡状态的弛豫过程,又可作为线圈记录的电磁信号进行测量。测量得到的电磁信号的初始振幅(在射频激发之后)与质子的总量有关,故而该方法可以估计材料中的水分总量。如Barakat等就使用了专门的高温核磁共振装置直接无损测量了浇注料在初次干燥阶段(100~300℃)的内部水分分布和温度分布,并从测量结果中得到了干燥前沿的速度与温度等信息,再对所得数据进行总结、分析、归纳,得出了干燥行为的线性函数关系等重要结论,有助于相关研究者进一步理解浇注料的干燥和爆裂行为。由于X射线的信号衰减与材料密度相关,而在浇注料中坯体与孔隙(包括其中的水)的密度是截然不同的,因此可以通过X射线的衰减变化来直观观察材料内部的含水量变化。将观察到的结果与温度分布相结合,还可以得出关于内部压力的相关结论,也就是说X射线CT的测试可以获得许多信息以帮助实时研究浇注料的内部状况。如文献就使用了X射线CT、1H-NMR技术对混凝土中的水分迁移行为进行研究,并通过X射线CT原位观察到了“水分阻塞”现象。中子照相技术也被认为是表征材料内部水分分布的有效方法之一。这是因为浇注料中的骨料和无水水泥与中子的相互作用较弱;而水化产物及填充有水的毛细孔与中子的相互作用则较强(主要由于中子散射),所以后者会导致入射中子束的强烈衰减而与前者的结构显著区分开来。如Toropovs等就使用了中子照相技术实时研究了模拟火灾的高温时高性能混凝土中的水分分布。中子层析成像研究水分分布的原理也基于氢原子对中子束穿越时的显著吸收,这个吸收过程会导致透射中子束强度的大幅衰减,因而在研究材料内部的干燥前沿时十分有用。根据Dauti等的报道,这是一种创新性方法,其最突出的特点就是能够对水分分布进行原位三维分析;此外,该方法还使用了具有高中子通量的新型成像仪器Ne XT,故可以在1 min内获得高质量的断层照片,并能以足够高的分辨率(能够捕获关键局部异质性)跟踪高温下相对快速的脱水过程。而就是在此项技术的帮助下,这些研究者直接证明并量化了混凝土样品中的“水分阻塞”现象。将同一样品的中子层析成像和X射线CT图像进行对比(图6),容易发现X射线CT更适合检测孔隙(因为其密度较低),但无法将基质/骨料区分开来(二者密度和原子序数相当)。相反地,在中子层析成像中,骨料对中子来说几乎是不可见的(吸收少),这使得其与基质的区分变得更加容易,同时又阻碍了骨料与孔隙的区分。中子成像这一特征使在真实的浇注料(混凝土)坯体样品中原位研究基质中的水含量变化成为可能。各检测手段见表4。
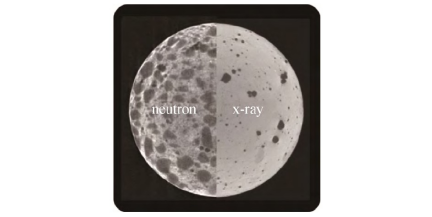
图6 同一样品的中子层析成像和X射线CT图像对比[55]
表4 浇注料干燥过程检测手段小结
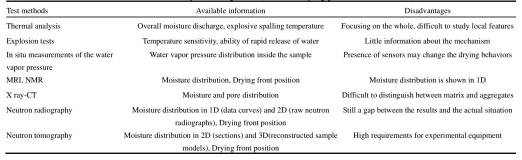
5 浇注料干燥过程的模拟
虽然在进行实际试用不可行时,可用模拟实验结果指导工业实践,但是模拟过程与实际工况间毕竟存在差异,这就会导致有时实验室测试结果与工业使用结果不符。而将实验室样品测得的参数通过物理/数学推导建立起数值模型再对实践进行指导(即由实践经验指导转向系统理论指导),就会由于模型自身的理论可靠性一定程度上解决这个问题。而干燥过程数值模型的建立不仅可以直接为大块坯体安全加热曲线的设计提供指导,还可以帮助相关研究者理解导致爆裂发生的机制,因而也得到了一些学者的关注。目前,对浇注料干燥过程数值模拟的专门研究才刚刚起步[50,56,57],但是针对此类高温下部分饱和的多孔介质中水分输运的问题已经建立了许多有影响力的模型(原用于模拟火灾中混凝土的脱水行为),如Luikov模型、Bažant模型、Tenchev模型、Gawin模型和Dal Pont模型等[7]。在这些模型中,最简单的Bažant模型需要9个输入参数,其中仅有6个参数需要测试材料得到,而其特征描述的相对简单也使其成为了相关领域中最常用的模型之一。但是该模型获得的信息有限,使其难以用于对机理的详尽理解;而且,在简单模型中参数测量准确度对可靠性的影响可能比复杂模型中更为显著。而对于理论上最精确的Gawin模型和Dal-Pont模型,共需要29个参数,其中,10多个都需要通过测试材料来确定,这就给模型的实际应用带来了困难。这些基于经典不可逆热力学(CIT)推导出来的数值模型,大体上都遵循“模型复杂度”、“输出信息(参数)量”、“必需输入信息(参数)量”三者正相关的关系。所以在解决实际问题时研究者仍然倾向于使用具备足够精度的简单模型,如Moreira等[57]指出简单的单相模型与复杂的多相模型计算出的结果类似,又考虑到计算效率及复杂模型对输入参数的要求,所以前者在模拟浇注料的干燥中具有更大的实用价值。数值模拟在浇注料干燥中未来的应用发展,应该是在保证易用性的前提下获取更高的模型精度。为此,首先可以采取折中的思路,尽量在“模型精确度”(科学性)和“测试复杂度”(技术可行性)间取平衡,找到一个兼顾的方法,如使用中间复杂度的Tenchev模型,或者可以通过将影响较小的参数视为常数来进行简化;其次,从材料基础数据收集与利用的角度,建立并使用相关材料数据库也可以有效减少在建模时需要测试的参数数量。而由浇注料防爆裂各研究领域间的关系(图7)可知,为了对模型更好地进行验证,也需要对材料测试技术继续进行研究(如对基准参数测试的改进)。另外,与具备丰富相关经验的其他领域(如高温混凝土)研究人员进行资源整合也可能有利于对浇注料干燥行为的深入研究。
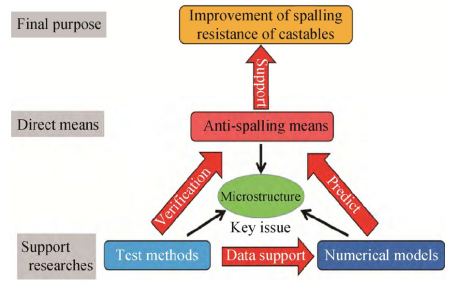
图7 浇注料防爆裂相关研究的示意图
6 展望
浇注料的使用有利于耐火材料的绿色化发展,而含水结合体系在过去、现在和可预见的将来都是浇注料结合体系中的关键部分。虽然该体系具备许多优点,但用其结合的浇注料在加热时都存在一定的爆裂风险。尽管目前关于浇注料中抗爆裂的研究已经取得了一定成果,但随着耐火行业对材料各项要求的不断提高,相关研究仍有继续深入的空间:
1)寻找室温下具备高渗透结构且综合性能满足所需的其他结合体系,如开发除二氧化硅外的其他氧化物溶胶等。
2)探索新型防爆添加剂,除了要开发适用面广的通用防爆剂外,也可以像氧化镁结合体系中一样,利用结合体系的特性进行微结构精细调控,从而开发出专用防爆剂。
3)改进已有的测试手段,并努力利用/开发新的测试手段,为浇注料干燥(爆裂)过程的精细表征和机理研究的未来发展提供技术支持。
4)进一步深入研究浇注料的干燥(爆裂)机理,并开发出更具科学性的数值模型;另外,降低现有数值模型对材料参数测试的要求,从实际应用方面考虑也具有相当价值。